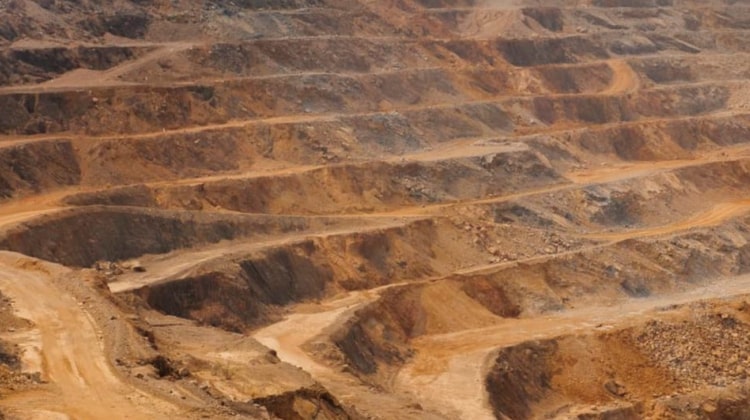
Looking back on the history of mining and up to present-day techniques, many advancements have occurred in the way mined materials are extracted. Heavy-duty, durable and compact mining equipment has increased cost-effectiveness and the efficiency with which we mine. As a result, the mining industry has been able to reduce waste, as well as dangerous chemicals.
Compared to tin mining the history of zinc mining is relatively short. In the 18th century, it was discovered that sphalerite, or zinc sulfide, could be smelted into brass, resulting in the first patented techniques. Since then, the zinc industry has progressed to the current zinc mining process and production methods used today.
From coatings to compounds, zinc is used in many areas of our lives. Whether it’s used in the home or an industry setting, zinc remains an important material. Under the below topics, there are many more specific ways in which zinc is part of our work and our lives.
Where is Zinc Found?
Although the largest zinc mine is the Red Dog Mine, located in Alaska, zinc mines exist in 50 countries around the world. Among these 50+ countries, the world’s largest zinc producers are Canada, Australia, China, Peru and the United States. A few zinc mines in Canada, Australia, Ireland and Namibia will close within this decade due to depletion. The major types of zinc ore deposits are generally found to be sediment-hosted, volcanic-hosted, intrusion-related, Broken Ore type or Mississippi Valley Type.
The Zinc Mining Process
The zinc mining process is conducted primarily underground, with more than 80 percent of all zinc extracted beneath the Earth’s surface. Eight percent of zinc is mined in open pits, with the remaining 12 percent being mined through both methods. Once it’s removed from the earth, the concentrate is roasted at a temperature of 950 degrees Celsius, causing zinc, sulfur and iron oxidization. After the zinc and iron oxides are reduced to powder form and leached with diluted sulfuric acid, the solution is neutralized and contaminants are removed via filtration. In the foundry, the zinc goes on to take its final form.
-
Next Post
Tin Mining and Processing
Related Posts
Ionosphere Investments Granted Export Authorization by Ministry of Mines and Mining Development
Ionosphere Investments Granted Export Authorization by Ministry of Mines and Mining Development Ionosphere Investments…
Driving Strategic Mineral Exploration for Sustainable Growth
CEO Statement Driving Strategic Mineral Exploration for Sustainable Growth As we approach the close of…
Lonosphere begins Spodumene Shipment from its Bluffhill Processing Plant
Ionosphere has reached two milestones, The first milestone is the start of the loading of…
Lonosphere begins lithium concentrates production
Lonosphere investments has begun lithium concentrates production at it factory in Harare, Bluffhill, Managing Director…