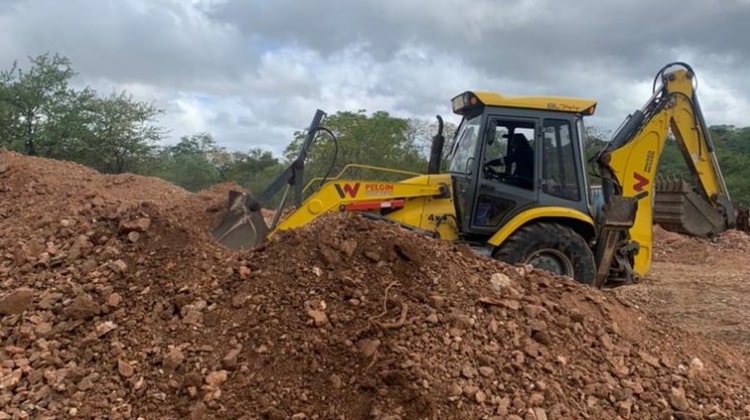
-
Previous Post
Zinc Mining and Processing
-
Next Post
Lithium Mining Processing
Lonosphere Investments is a leader in trading metals and minerals sourced from Zimbabwe. Built on detailed market intelligence, Ionosphere aim is to grow consistently with the same integrity that laid it’s foundation. We are committed to provide superior quality products to our customers.
Read More